Nanolithography
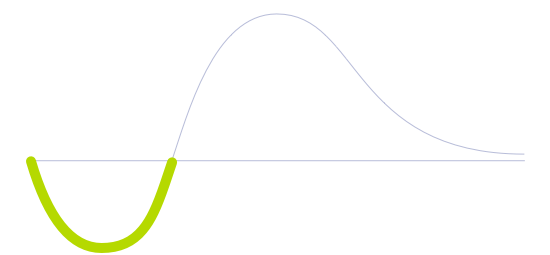
Technology Life Cycle
Initial phase where new technologies are conceptualized and developed. During this stage, technical viability is explored and initial prototypes may be created.
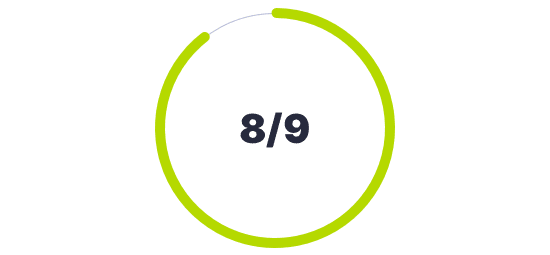
Technology Readiness Level (TRL)
Technology is developed and qualified. It is readily available for implementation but the market is not entirely familiar with the technology.
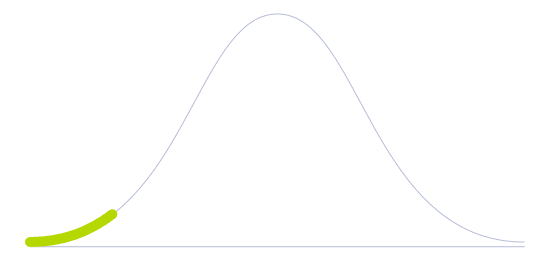
Technology Diffusion
First to adopt new technologies. They are willing to take risks and are crucial to the initial testing and development of new applications.
By working in nanoscale, the patterning technology of nanolithography is able to inscribe or print in less than 100-nanometer resolution patterns onto any surface and assist with microfabrication techniques —such as photolithography— for manufacturing a variety of chips. Photolithography uses photon particles to produce models, and nanolithography then borrows this technique to create patterns on a micro-or nanoscale. In one of this technology's variations, extreme ultraviolet beams can inscribe the mark onto the surface.
Nanolithography is a critical technology in the semiconductor industry, as it enables the production of smaller, faster, and more powerful electronic devices. It has also found applications in other areas, such as nanoscale sensing and imaging, biomedical devices, and the creation of new materials with unique properties.
Also known as a nano fountain pen or nano fountain probe, this solution could have applications in areas such as nanoparticle manometric deposition or the deposition of metallic lines and polymer molecules, where DNA molecular placement is of fundamental and considerable technological importance, thus becoming a faster and cheaper method for producing transistors and chips.
Future Perspectives
Since nanolithography deals with tiny scales and very sophisticated devices, the exactitude becomes a challenge for scientists. As the dimensions of the structures become smaller, the effects of quantum mechanics and surface interactions become more pronounced, requiring new approaches and techniques to overcome these challenges. Precision problems could result in manufacturing errors and the subsequent expenditure of materials and waste production. To allow the electron beam or light to trace a precise pattern, the way movements are translated into the stages of production need to be improved so that patterns are preserved entirely and without mistakes.
Nanolithography has the potential to revolutionize many fields by enabling the creation of structures and devices at the nanoscale level. For instance, it could be used as building blocks or stepping stones for quantum computers, such as superconducting qubits and nanoscale wires, which could enable faster and more powerful computing technologies. Other solutions, like nanorobots, could be created in fields such as medicine, manufacturing, and environmental monitoring.
Image generated by Envisioning using Midjourney